1 岗位职责
1.1 熟知本岗位的危险源,及时发现及消除生产中存在的安全隐患,并做好相关记录。
1.2 熟悉炉体各部位构造及各处的维修操作。
1.3 了解焦炉用砖及耐火泥的规格标准,及泥料配置的原则和方法。
1.4 紧密与调火工配合,搞好炉体维修,保证正常生产,延长炉体使用寿命。
1.5 按计划对焦炉进行日常维修、维护、喷补工作,认真填写维修记录
1.6 计划定期进行焦炉各部位的检查,并留有完整的记录。
1.7 完成焦炉临时非计划的抢修任务。
1.8 按规定时间对所属设备进行检查、维护、保养、加油和清扫。
1.9 负责耐火制品及耐火泥料的妥善保管。
1.10 不断加强技术管理工作,按要求建立健全并认真填写各种原始记录、台帐、报表等,及时归档。
1.11 保持所属区域卫生的清洁、整齐。
2 技术标准与规定
2.1 硅砖
2.1.1 化学成分:二氧化硅含量不少于93%。
2.1.2 物理性质:耐火度不低于1690℃;0.2Mpa荷重软化点不低于1620℃;真比重不大于2.37;气孔率不大于24%;常温耐压强度炉底、炉膛、炉顶不小于22Mpa/cm2,其它部位不小于17.5 Mpa /cm2残余膨胀温度在1450℃时,不大于0.8%。
2.2 粘土砖
2.2.1 化学成分:三氧化二铝含量不小于35%。
2.2.2 物理性质:耐火度不低于1670℃;0.2Mpa荷重软化点不低于1300℃;重烧线收缩1350℃时,不大于0.3%;显气孔率不大于24%;常温耐压强度不小于20MPa
2.3 低温硅火泥
二氧化硅含量85—90%,耐火度1580—1650℃。
2.4 粘土火泥
Al2O3+TiO2含量大于30—37%,耐火度1580—1710℃。
2.5 所用的耐火材料、耐火泥的物理、化学性质、粒度应符合技术标准,应有出厂合格证和必要的检验报告,不合格的泥料未经批准不能使用。
2.6 泥料应按热修部位和指定的配比进行配制,误差不超过5%,随配随用,泥料应配准确,搅拌要均匀,要掌握泥料的发泡时间,喷浆时要掌握泥料的重度。
2.7 泥料粒度要符合规定,调和泥料所用的水和工具要清洁,泥浆池、泥浆桶应加盖,泥料中不准混入焦末及其它杂物。
2.8 泥料中需要加入水玻璃时,应在使用前加入,其加入量按碱度计算;泥料中加磷酸时,应在24小时前配制;加入水泥的泥料,要在当天使用以免凝固。
2.9 泥料过粗有块时,应在配制前过筛,凡灌浆用泥料不能过稠。
2.10 泥浆在装入喷浆机前,要经过1—3mm筛子过滤去掉杂物,以免堵塞喷嘴。
2.11 大中修所用泥料,在使用前应检验,符合技术标准,才能使用。
2.12 操作的一般要求
2.12.1 喷补前应准备好工具、泥料、喷浆机,要先检查各开关是否灵活好用,管线是否畅通,泥料过滤后方可倒入喷浆机。
2.12.2 在修补时,先将破损处的旧砖、旧泥料、石墨等清除干净,新砌砖平整、牢固,与旧有物体吻合,灰缝内灰浆要灌满。
2.12.3 抹补泥料时,要均匀平整,一般喷补不应过厚,损坏严重处可在第一次喷补的泥料干固后,进行二次喷补。
2.12.4 操作时节约用料,修补工作完后,喷浆机和工具要清洗干净,并将现场清扫干净,废物运到指定地点。
2.12.5 对炉体各部位损坏变化情况的检查结果以及修补部位均应留有记录。
3 各部位泥料配比
3.1 炭化室
3.1.1 抹补
高铝火泥100%,混合土:生料=80%:20%;磷酸比重(1.4),每100千克泥料加10±0.5千克。
3.1.2 喷补
粘土细料80目以下,磷酸比重(1.4)每100千克泥料加40千克。
3.2 炉底灌浆:超过60mm深度时用粘土砖渣40%,粒度3—5mm;粘土火泥60%0—1mm,磷酸比重(1.4)100千克料加30千克。
3.3 炉门框灌浆
低温硅火泥 :结合粘土=4:1
3.4 砖煤气道灌浆:80目以上低温硅火泥加结合粘土(4:1)。
3.5 封墙勾缝:纯粘土100%加水玻璃8%。
3.6 更换除尘口、更换看火眼、炉顶勾缝:粘土火泥100%,水玻璃2%。
3.7 废气盘保温
抹底:粘土60% 水泥20% 河沙20%
抹面:水泥30% 白灰40% 麻刀灰0.5千克 海泡石加水泥10%
3.8 修补操作台
500#水泥:沙子:石子=1:2:4
3.9 上升管底座:100%粘土火泥。15%水玻璃
3.10 桥管接头:用有尘φ32mm编织石棉绳塞严。
3.11 修补炭化室:中温硅火泥100%,每100千克加20千克磷酸。
3.12 砌筑炉门衬砖:粘土火泥100%加水玻璃8%。
3.13 炉顶灌浆:粘土火泥100%。
4 热修维护制度
4.1 炉墙检查
4.1.1 炉墙是否有变形、孔穴、裂纹、凹凸、漏缝、烧熔、剥落、灼烧、石墨等现象及其它缺陷,并做详细记录。
4.1.2 炭化室底部的磨损情况,炭化室底部、炉门框、炉头砖、磨板之间严密情况,烘炉孔塞子砖严密情况,并做详细记录。
4.1.3 炭化室局部抹泥剥落情况,分严重、重、轻做记录。
4.2 炉顶检查
4.2.1 除尘孔倾斜、变形、断裂、凸起情况,除尘孔底部砖的剥蚀情况。
4.2.2 上升管座砖的泥土剥落,冒烟着火及时灌浆严密。
4.2.3 看火孔座松动、断裂及漏火及时处理。
4.2.4 炉顶平面出现塌陷应立即灌浆或翻修。
4.2.5 除尘车轨道、轨枕是否断裂、空洞必须要修理或灌浆。
4.2.6 小炉头松动、漏气、着火应马上处理。
4.3 蓄热室检查
4.3.1 单叉部必须严密。
4.3.2 测温孔、测压孔要完好。若有松动或破损及时处理。
4.3.3 封墙保持严密,内部不许串漏,顶部格子砖有无烧坏变形
4.3.4 废气盘保温层剥落,马上修补。
4.4 操作台检查及其它
4.4.1 炉门下坎砌筑严密完整。
4.4.2 操作台轨道根部要严密。
4.4.3 台面面砖要完整。
4.4.4 焦炉各处要严密,防止漏水或杂物掉下。
4.4.5测压导管、测温孔的松动检查
4.5 燃烧室的检查
立火道内要清洁、清晰,没有混浊。
5 焦炉各部位的热修操作
5.1 更换除尘孔砖及铁圈
5.1.1 在结焦末期进行,更换前,关上该号桥管翻板,打开上升管盖,再打开炉盖,拿掉旧炉口圈及旧砖。
5.1.2 将炉口处清扫干净,用泥浆抹平后,放好炉口砖,打上灰浆,放好铁圈,与炉口砖靠紧找平,使之稍低于炉顶表面,并灌浆严密
5.1.3 在操作过程中,铁圈及砖、泥浆等杂物,不要掉入炭化室内。
5.2 密封上升管根部
5.2.1 用风将上升管根部旧的填充物清扫干净,用水润滑周围。
5.2.2 用浸透水玻璃的石棉绳缠入上升管根部,用铁钎塞紧压实、压平,直至不冒烟为止。
5.3 密封桥管承插口
先清除干净旧的填充物,塞入石棉绳,用钎子打严压实。
5.4 翻修小炉头
5.4.1拆除旧砖,用风吹扫干净。
5.4.2 保护板灌浆灌满为止,塞入浸有水玻璃的石棉绳,要塞紧,并用灰浆抹平,重新砌上小炉头砖,砌时灰浆要饱满。要分别砌筑,每个炉头之间用一条直缝分开便于再次检修小炉头。
5.4.3 砌体表面平整,外部表面要二次勾缝,其标高应低于炉体表面。
5.5 炉顶表面灌浆
5.5.1 用压缩空气及勾子将砖缝内的煤粉、焦尘等杂物清扫干净。
5.5.2 采用间隙式灌浆,以达到灰浆饱满。灌浆时打开看火孔盖检查,以防泥浆漏入立火道中。
5.6 修理拉条沟及盖砖
5.6.1 拉条沟盖砖不平,应及时抹平。
5.6.2 在更换拉条前,先拆除拉条沟的盖砖,松动拉条内的填料。
5.6.3 等铁件组抽出拉条后,将拉条沟用风清扫干净后灌浆。
5.6.4 拉条装入后,填断热粉,砌上拉条沟盖砖。
5.7炭化室炉墙的喷补
5.7.1 喷补前将炭化室墙上面的石墨清扫干净。
5.7.2 喷浆机风压应保持在0.15—0.2Mpa,喷嘴距炉墙150—250mm。
5.7.3 破损严重的部位,喷完一次泥浆后要第二次喷补,泥浆厚度不得超过5—10mm。
5.8 炉头抹补
5.8.1 提前打开上升管盖,推焦后进行抹补。
5.8.2 用铁刷子将炉肩缝隙的石墨及灰缝清扫干净。
5.8.3 在砖缝处喷一层薄薄的磷酸泥料,约为2—3mm厚,便于挂结泥浆,喷补时,喷嘴距炉墙150—250mm,角度为30—40°,喷杆移动速度要均匀。
5.8.4 将前一天配好的磷酸泥料抹于砖缝表面,用抹子压挤、使灰缝泥料压实压平,抹后再喷一次浆。
5.8.5 将炉门下部剩余泥料及焦炭清扫干净,对上炉门。
5.9 修补炉底砖
5.9.1 焦炭推出后,用耙子将残余焦炭扒出,用风将凹陷处底焦末吹干净。
5.9.2 将磷酸泥料倒入凹陷处,然后抹平,如果陷处太深,将掺有骨料磷酸灰浆倒入凹陷处,用专用工具压实、压平。
5.9.3 损坏严重者炉层砖厚度小于40mm,应将废砖铲掉,重新砌砖,接缝要平,不能有反茬。
5.9.4 对上炉门15—20分钟后再装煤。
5.10 更换炉门框的操作
5.10.1 准备工作
5.10.1.1 将炉门、新炉框固定好,按规定粘好石棉绳。
5.10.1.2 安装好吊装环,将需要加工的凸台加工好。
5.10.1.3 新炉框就位。
5.10.1.4 欲更换号前一循环少装煤。
5.10.2 更换工作
5.10.2.1 提前摘炉门凉炉。
5.10.2.2 摘掉磨板。
5.10.2.3 用旧炉门对好旧框,固定好安全吊装环。
5.10.2.4 割除钩头螺栓,用取门机摘掉旧框。
5.10.2.5 新框用取门机对好,上好钩头螺栓。
5.10.2.6 上好磨板,灌浆、抹框、清理现场。
5.11 燃烧室炉头一二火道的翻修
5.11.1 翻修条件
在炉头产生通长宽达40—50mm墙砖碎裂,墙面凹入40-50mm,凸出20—25mm有倒塌的危险,用喷补、抹补无法解决时应翻修。
5.11.2 翻修前硅砖预热到40—50℃,准备好所需工具和硅砖泥料及必须的劳保用品。
5.11.3 预先通知装煤人员在所翻修侧要少装煤,在修炉过程中相邻炉子不能出炉。
5.11.4 装煤12小时后,打开上升管盖,关上翻板,摘下炉门,扒出炉头焦炭,通知调火切断有关火道的煤气进行局部降温。
5.11.5 砌上隔热封墙,其位置在翻修处里边300mm。
5.11.6 拆除旧墙前,先将铁盖板盖在斜道口上,由下至上,拆除旧墙但不能用力过猛,以免震动其它未损部位。
5.11.7 在砌完前,要将立火道底部清扫干净,斜道畅通,并取掉斜道覆盖铁板。
5.11.8 砌上新砖,对旧墙损坏处进行抹补、喷浆,如果损坏较大应用支撑器顶住损坏面防止在烘炉过程中新砌墙面变形。
5.11.9 扒除封墙、对上炉门,何时推焦听调火人员通知。
5.11.10 通知调火,恢复有关火道加热。
5.11.11 质量要求
5.11.11.1 砖缝内灰浆饱满,墙面平整。
5.11.11.2 卧缝与旧墙间立缝最大不超过10mm,与旧墙接头的新砖长度不能小于150mm。
5.11.11.3 砌完后,将立火道、斜道、蓄热室顶部清扫干净。
5.12 蓄热室封墙修补
5.12.1 如蓄热室封墙有小缝,可采取表面勾缝或刷浆方法。
5.12.2 如大砖或封墙损坏严重时,以及凸出30mm以上的,要拆除重砌,更换大砖的工作要在下降气流时进行。
5.12.3 翻修外部封墙时,要先对内部封墙细致勾缝。
5.13 单叉部与小烟道接口处的抹补
5.13.1 外表有小缝要及时密封,可用勾缝刷浆方法。
5.13.2 当修补连接口时,应把旧泥料和石棉绳铲除,用沾有水玻璃的石棉绳塞紧缝隙,再用泥料抹平、抹严并刷浆。
5.14 喷补小烟道
5.14.1 喷补在上升气流进行。
5.14.2 风压控制在0.1—0.15Mpa,不要将泥浆喷到格子砖、篦子砖上。
5.15 更换蓄热室测温孔座
取下旧测温孔座,将砖周围清扫干净,将新测温孔座缠好石棉绳沾上泥浆,安好找正、四周用泥料密封好。
5.16 喷补砖煤气道
5.16.1 关闭加减旋塞,切断煤气。
5.16.2 用钎子通透砖煤气道,用玻璃片,挡住支管下口,观察是否通畅及漏火。
5.16.3 用布将喷浆管缠好,插入砖煤气道,并用力向下拉紧,用布把立管堵严,以防漏浆或浆液进入横管。喷浆时风压保持0.08-0.1MPa.左右,喷浆泥料应均匀一致(比重约为1.14-1.15左右)。
5.16.4 向上压浆并计算,估计浆过窜漏地点即可,注意不要将泥料喷入立火道内。
5.16.5 喷补完毕用铁条捅透砖煤气道。
5.16.6开正煤气旋塞恢复加热。
5.16.7 去炉顶观察火焰燃烧情况。
5.17 喷补斜道
5.17.1 用焦炉煤气加热时,在上升气流进行,通知调火工给予协助工作。如一个交换完不成时通知调火工关闭该号煤气旋塞。
5.17.2 喷补时,应注意不要将泥浆喷到格子砖和斜道口上。
5.17.3 喷浆完毕,拿出铁板,砌好封墙。
5.18 蓄热室格子砖更换
5.18.1 更换前与调火工联系采取必要的降温措施。
5.18.2 废气盘用铁板盖上,两端铁架子、跳板放牢固。
5.18.3 拆除封墙,若上部分大砖松动,用木楔子塞紧。
5.18.4 格子砖一层一层的扒到底,扒除三层后,铺上铁板,再进行拆除,当扒完4-5层后,将看火孔盖打开。
5.18.5 全部格子砖取出后,打开清扫孔,将小烟道和篦子砖清扫干净。
5.18.6 用铁板将篦子砖盖住,进行主墙的喷补。
5.18.7 抽出铁板,按设计要求装入新的格子砖,当装入第五层后,可按阶梯型装入。
5.18.8 装完格子砖经检查合格,砌上封墙。
5.18.9 质量要求
5.18.9.1 墙面斜道口喷补好,清扫干净。
5.18.9.2 格子砖完整、清洁、装平靠紧,格子砖对正,最底层偏差不大于20mm。
5.19 吹扫蓄热室格子砖
5.19.1 吹扫应在检修时切断电源后操作。
5.19.2 在下降气流时进行,打开清扫孔,将风管插入吹扫。
5.19.3 吹扫至交换前2分钟关闭风管旋塞,抽出吹扫管,待下降时继续吹扫。
5.19.4 风压在0.35MPa以上。
5.20 炉顶表面局部修理
5.20.1 拆除炭化室顶部表面砖、除尘孔砖、看火孔砖,用砖盖好立火道,不允许杂物掉入火道内。
5.20.2 将炉顶表面清扫干净。
5.20.3 先砌除尘孔砖、看火孔砖,后砌炭化室顶部。
5.20.4 砌时要拉线,找好中心,要求表面平整,炉口略高于炉顶表面,炉顶中间和边要有坡度。
5.20.5 炉顶表面缝要用掺有水泥的粘土火泥进行二次勾缝。
5.21 更换上升管
5.21.1 在推焦前进行,要求装煤时间超过规定时间2/3以上。关上桥管翻板,打开除尘孔盖,立临时小烟囱。
5.21.2 拆除桥管接头处的填料,吊起桥管、卸下旧管。
5.21.3 将座清扫干净,安装新管及桥管,密封好各处接头。
5.21.4 拆除临时烟囱。盖好盖,打开翻板,恢复正常生产。
5.22抹补干燥孔
检查和抹补时要与炉顶操作工联系好,在两侧炉门对好后进行,每次只能打开一个盖,灰浆脱落及时抹补。机焦侧炉头处干燥孔在推焦前摘门后抹补。
5.23 更换炉门衬砖
5.23.1 根据炉砖的损坏情况,局部或全部拆除、清扫干净。
5.23.2 砌新砖时,应由下而上进行,必须紧紧地砌上隔热层,用泥料塞紧压实砖缝。
5.23.3 严格控制外形尺寸,不要超过±5mm。砌砖后,应彻底全面勾缝。
5.24 修炭化室熔洞及灰缝
5.24.1 一般在墙内出现碎裂剥落及没有穿洞的喷补。
5.24.1.1 事先与出炉操作工联系好,并清除需喷补部位的石墨等物。5.24.1.2 先开风机吹扫喷补部位,然后喷浆,喷浆杆在炉内移动的快慢应一致,喷浆厚度一次不超过5mm,如需多次喷,只能在上次盖层加热至赤色后方能进行。
5.24.1.3 喷浆机风压为0.025-0.03MPa,喷浆时间不超过5分钟,一次推焦后喷上的泥料层厚度不超过3mm。
5.24.1.4 喷完浆后,扒净掉在炉顶的灰浆。
5.24.1.5 修补后20分钟后再装煤。
5.24.2 炭化室处出现裂缝较小的熔洞时的抹补。
5.24.2.1 采用磷酸泥料抹补,推焦后,将修理处清扫干净。
5.24.2.2 在抹前应先喷磷酸浆,以后抹泥和喷浆交替进行,每次抹补的泥料层应均匀,及时用铲子将泥料压紧,所用铁铲必须在泥料表面能够移动而不粘结泥料。
5.24.2.3 抹的墙面应低于炉墙。
5.24.3 炭化室、炉底已有洞时的挖补。
5.24.3.1 根据损坏情况,先必须制定挖补方案。
5.24.3.2 洞口处的坏砖应及时处理干净。
5.24.3.3 严重的用钢钎打掉一部分。
5.24.3.4 将新砖预热,按洞形加工,使其外形比熔洞小10mm左右抹上泥浆用托板送至洞口,用抹子迅速把砖推进熔洞里。
5.24.3.5 最后对补处进行喷浆,升温后方可装煤。
在上述操作中,进入火道中的煤及灰浆均由道口清除,用铁板放在格子砖上取出,煤粉需用“气老虎”由看火孔处抽出。
6 热修库房管理要求
6.1 耐火材料的贮存,要有单独分类的灰库,盖顶四周要严密,防止雨雪、灰尘、焦沫落在耐火材料上。
6.2 仓库要有防火,排水设施,有自来水、下水道,照明要充足完善。
6.3 来料要说明日期、数量、产地及化学成分,每来一批料,要交化验室进行化验。
6.4 磷酸要有专门贮放设备 ,以免杂物落入变质,接触磷酸的容器应耐酸,不可将酸注入水泥池内。
6.5 操作者使用完工具,应刷洗干净,放回原处。
7 喷浆机的使用
7.1 喷浆机压力的使用应根据泥浆的比重和所修部位等确定:喷炭化室为2—4 kg/cm2;砖煤气道0.5—1.3 kg/cm2;喷浆机最大工作压力不大于4 kg/cm2。
7.2 喷浆机装有压力表,一般不允许超过规定压力,喷浆杆移动要自上而下,喷嘴与炉成45°角,喷补不宜过厚,熔洞过大时要喷、抹结合,喷补部位用铁铲(砖煤气道用铁钎)将残渣清扫干净。
7.3 在使用前应详细检查各接口的严密性,胶管有无开裂,压力表是否完好。
7.4 据不同部位,专人负责喷浆机风压。
7.5 喷浆机用的浆必须过筛后,方可倒入喷浆桶内。
7.6 喷浆时,必须先开风后给浆。
7.7 喷浆完毕,要先关送浆开关,待风将胶皮管及喷嘴里吹净,再关风,及时将机内残风放出。
7.8 工作完毕后,将桶和送料皮管及喷浆机清扫干净。
7.9 喷浆机使用中喷嘴禁止对人。
8 焦炉各部位维修泥料配比、检查部位
8.1 焦炉经常维修项目及各部位热修泥料配比(表1)
部位 |
炉顶 |
炉台 |
蓄热室 |
|||||||||||||||||||
比例 |
炉顶灌浆 |
砌小炉头 |
换看火眼砖及铁圈 |
换表面砖及灌浆 |
上升管衬砖及底座 |
上升管根 |
桥管接头 |
拉条沟 |
喷炉头墙 |
喷炉头墙 |
抹炉头墙 |
抹炉头墙 |
修补炭化室底砖 |
砌地角砖 |
保护板 |
修抵抗墙 |
喷小烟道 |
喷砖煤气道 |
蓄热室封墙砌砖 |
蓄热室封墙勾缝 |
||
耐火材料 |
||||||||||||||||||||||
粘土熟料 |
70 |
100 |
100 |
|||||||||||||||||||
粘土火泥 |
100 |
100 |
100 |
100 |
100 |
100 |
100 |
100 |
100 |
100 |
100 |
100 |
100 |
100 |
100 |
100 |
100 |
|||||
精矿粉 |
30 |
|||||||||||||||||||||
高温沥青 |
100 |
|||||||||||||||||||||
硅藻土 |
100 |
|||||||||||||||||||||
磷酸 |
22 |
18 |
10 |
喷补22 |
||||||||||||||||||
水玻璃 |
5 |
15 |
15 |
石棉绳沾泥桨 |
5 |
15 |
20 |
15 |
20 |
20 |
5 |
15 |
15 |
10 |
20 |
|||||||
水(Kg) |
25 |
35 |
5-6 |
10 |
24-25 |
喷补24-25 |
①表中水玻璃、磷酸均为外加量。
②喷补用磷酸量按浓度40%,比重1.26计;抹补用磷酸按68%,比重按1.5计。
③水玻璃用量按碱(Na2O)14%计算,炉门框灌浆时,硅砖炉头用硅火泥,高铝砖炉头用粘土火泥。
④小烟道清扫抹补,堵砖时与抹立管根部基本相同,但精矿粉改用水泥。
8.2 硅火泥粒度组成(单位mm)(表二)
粒度 单位 组成 <0.077 <0.10 <0.2 <0.44
组成 % 68-70 84-88 90-94 >99
8.3 粘土火泥理化指标(表三)
NF--38 NF--34 NF--28
耐火度℃ 1690 1650 1580
水分含量不大于% 6 6 6
8.4 三级粘土火泥的粒度(%)(表四)
通过筛孔 细粒 中粒 粗粒
0.125mm不小于 55 25 15
0.15mm不小于 97 -- --
1.00mm不小于 100 97 --
2.00mm不小于 -- 100 97
2.80mm不小于 -- -- 100
8.5 各部位检查及维护制度(表五)
序号 项目 检查周期 修补时间 备注
1 焦炉顶面砖 每月一次 及时修补
2 看火孔\除尘孔\铁圈 每天一次 及时修补
3 上升管底座及衬砖 半月一次 及时修补 根部半年全面灌浆一次
4 桥管插口接头 每天一次 及时修补 每年全面翻修一次
5 小炉头的检查 每天一次 及时修补
6 炭化室及炉头墙的严密性 每月一次 计划修补
7 炭化室底砖 三个月一次 根据损坏程度列计划检修 每年用压缩空气吹扫检查一次
8 炉门框及炉肩缝隙 半月一次 及时修补
9 炭化室上、中、下宽度 每年一次 上报车间处理
10 蓄热室封墙 每月一次 及时修补 半年一次全面勾缝
11 废气瓣底座 半年一次 按计划处理
12 废气瓣与小烟道连接处 半月一次 按计划处理
13 砖煤气道、斜道、小烟道的检查 三个月一次 及时修补 调火配合特殊情况抽查
14 病号炭化室、蓄热室的检查 一周一次 视情况而定
15 蓄热室全面检查 每月一次 及时修补
16 燃烧室全面检查 三月一次 及时修补
17 炭化室全面检查 半年一次 及时修补
18 抵抗墙全面检查 半年一次 视情况定
19 焦炉各部位砌体全面检查 一年一次
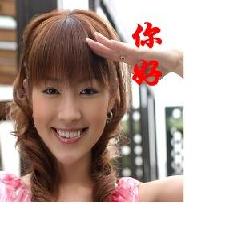
9.1 劳保用品必须穿戴齐全,方可上岗。
9.2 使用磷酸时,严禁将水注入酸内,而应将酸注入水内。
9.3 使用磷酸时,要防止酸液溅到皮肤上,造成烧伤。
9.4 禁止使用不清洁的放泥料用具或成分不明的耐火材料。
9.5 工作时,禁止将铁器掉入炉内。
9.6抹炉和清扫,要站在炭化室侧面,防止焦炭倒塌,并与司机、上升管工联系好,要注意来往车辆及照明电线。
9.7 炉顶操作时,要注意消烟除尘车走向,注意打开的除尘口,操作时,要站在上风口,不准坐在轨道上休息。
9.8 所使用的任何工具、拆下的东西,要放在安全地点。
9.9泥料的配制应仔细,按配比配合,不准估量。
9.10 严禁从炉顶、炉台向下扔东西,必须扔时,要有专人监护,防止伤人。
9.11 使用长工具时,要注意别碰别人和照明电线及滑线。
9.12 在地下室工作关闭旋塞后,工作完毕要开正。
9.13 在任何工作完毕后,要将现场清理干净。
9.14 高空作业要佩带安全带。
9.15 在地下室和烟道通廊处,不准随便动火、吸烟,要动火时,须持有动火证明,并有动火措施。
9.16 在蓄热室部位工作时,要注意交换设备运转。
9.17 热修操作时要防止被烧热的工具烫伤。
9.18 在地下室工作要与交换机工打好招呼。

易安博客 版权所有