
北京首钢氧气厂(以下简称“氧气厂”)是首钢总公司的生产辅助厂,也是首钢总公司搬迁调整、压产减产战略布局中的分厂之一。该厂年产氧气70多万t、氮气81万多t、液氩3万2896t,担负着首钢总公司炼钢厂、炼铁厂等单位钢铁生产用氧、用氮、用氩的供应任务。主要生产经营氧气、氮气、氩气、氦气、氖气、氪气、氙气、液氧、液氮、液氩、医用氧11种气体或液体产品。生产过程中具有高压、低温、易燃、易爆、易窒息等特点。
2008年,氧气厂还面临着如何处理好保障安全生产与设备检修维护、异地制氧工程建设、支援异地人力资源、职工思想波动、分流安置等一系列问题。氧气厂安全生产工作的好坏,不仅关系到自身的正常生产,还会影响到首钢其它分厂的生产需求,影响到首都的声誉。因此,氧气厂的生产安全,始终是全厂各项工作的基石。在不同层次的干部职工会议上,厂领导班子始终强调:“安全发展是完成各项生产、经营、建设工作的前提!安全工作是一条没有终点的路!长抓不懈、警钟长鸣是我们安全管理工作的基点。”
抓教育 提素质
为了抓好职工的安全技能和安全意识,几年来,厂安全管理部门围绕氧气厂生产过程中存在的高压、低温、易燃易爆、易窒息等危险因素,开展了旨在提高职工安全管理水平、安全消防技术、安全生产意识、安全综合技术素质、事故防范能力等不同目的的教育培训。
2007年,全厂组织开展了10期安全管理培训班,由主管厂长挑选典型的工业气体行业事故案例,进行讲解、分析、学习、吸取,累计有260名管理人员和班组长参加了培训。同时,重点开展了特种作业人员教育培训,先后数次组织气瓶充装、压力容器操作、安全押运等特种作业教育培训和考试取证,102人通过培训学习,取得了相关特种作业上岗资格。
培训中,厂里还坚持“走出去、请进来”的安全管理方式,聘请同行业专家、医疗救护专家、消防安全专家、职业病防治专家、特种作业管理专家、交通安全管理专家进行授课。培训后,厂里充分利用电视录像、黑板报、厂简报和安全知识竞赛等载体或形式,学习、巩固教育培训效果。
厂里还结合奥运会期间对危险化学品运输的特殊要求,开展了危险化学品安全运输教育培训,36名专(兼)职机动车驾驶员,详细地学习、重温了《道路危险货物运输管理规定》《危险化学品安全管理条例》等法规标准。同时,厂里还针对危险化学品生产特点及外来危险化学品运输车辆较多、进出频繁等实际情况,开展了进厂客户驾驶员教育培训,先后有280人次进厂客户驾驶员接受了培训。在此基础上,厂里还为危险化学品运输车辆配备了警戒线、警示路椎等安全防护器材,强化了危险化学品运输车辆“三检制度”。
勤检查 除隐患
面对生产供气压产,异地制氧工程建设及经营生产的新变化,为了确保在线制氧设备的正常运行,不发生各类事故,保证氧气厂生产经营顺稳进行,氧气厂积极开展了多种形式的安全检查,及时消除各类生产隐患。
组织开展了检修、抢修以及外委施工的各项安全检查工作。2007年,共制定3万制氧机组大修,氧气减压阀组、2号涡轮、3万分子筛检修,氢气站动力厂打井作业,球罐检测工作安全措施6项。特别是组织对3万制氧机组大修、3.5万制氧机组抢修等重点施工、检修、抢修工作现场,进行高密度、全方位的安全检查。同时,还结合检修活动,对厂内管辖的31.9km压力管道进行了在线检测,对78台在用压力容器、151个安全阀门进行了定期检测检验。对检查中发现的问题,及时组织精干人员进行整改,确保了各项检修、抢修工作期间未发生人身伤害事故及火灾火险事故。
组织开展了日常安全检查。按照氧气厂《安全检查制度》《消防安全管理规定》等规章制度,厂里坚持开展了日常安全检查。2007年,全厂通过安全检查,投入隐患治理资金120余万元。在对违章行为单位和个人进行处罚的同时,还奖励及时发现问题的职工5.2万元,检查中,组织更换了厂外、厂内道路限高标志牌36块和相关警示标识牌。
组织开展了重大危险源安全检查。氧气厂是北京市和首钢的重点防火单位及安全生产重点监控单位,涉及到氧气、氮气、氩气以及各种稀有气体的生产、储存、运输、使用多个环节。为了应对在设备设施出现故障停车,突然发生断水、断电或机械、电气故障时,确保向炼钢、炼铁高炉等用户单位持续供气,同时确保在用户需要加大气体用量时,能够达到“消峰填谷”的要求,氧气厂里还设有液体储罐3个,分别储存有3000m3液氧、1000m3液氮、200m3液氩;另外设有气体储罐2个,分别储存有600m3氧气、600m3氮气。这些储罐都是重点监控部位,为此,检查中厂里又重点检查了危险源控制措施的落实情况和职工安全规程的执行情况。
此外,厂里还在“春节”“五一”“十一”“元旦”“十七大”“奥运测试赛”等重大节日或重大活动期间,组织开展了专项安全检查。结合季节变化特点,开展了春夏季防触电,秋冬季防风、防滑、防坠落等安全检查。2007年通过安全检查,处理了各类生产隐患,实现了安全、火灾事故为零的目标。
预想预测 提前防范
制氧行业中极易发生中压氧气管道燃爆、高压氧气瓶燃爆、低温液体冻伤、人员氮气窒息、保温材料珠光砂埋人致死等事故,如果对这些危险因素认识不清、控制不好,则极易发生人身伤害和设备损毁事故,轻则影响企业正常生产,重则威胁职工生命安全。为此,加强危险源监管监控,成了氧气厂安全工作的首要任务。
为了有效预防这些事故,氧气厂按照危险化学品安全标准化工作要求,先后制定、修订、完善了《氧气厂安全生产责任制》《氧气管道、氮气窒息、气瓶作业危险部位、危险作业控制办法》《氧气厂危险作业安全管理办法》《氧气厂职业健康监护管理办法》等30多个安全生产和防火管理制度,在此基础上,厂里还将重大危险源的调查、辩识、界定,作为杜绝和减少重大生产事故、险兆事故发生的重要手段,组织全厂专业部门、岗位职工和生产经营协作单位,广泛开展危险源的辨识和风险控制。为了保证高压储罐区的安全,厂里按照国家《压力容器安全技术监察规程》以及氧气厂《技术操作规程》《设备维护使用规程》《安全规程》,进行了严格的控制、管理、操作、检测。同时,对照GB18218-2000《重大危险源辨识》标准,根据实际情况进行分析辨识,将其定为厂级危险源点进行控制,并制定了相应的措施。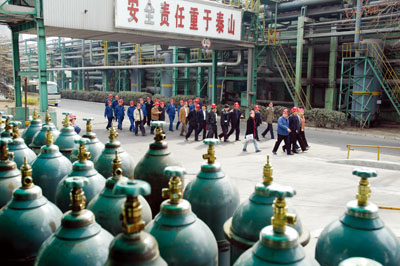
2007年,全厂共辨识、界定出B级危险源点3个,C级危险源点9个,危险控制部位19个,防火重点部位7个。
此外,氧气厂还在职工中广泛开展了事故预想预测活动,强化了对辨识出的危险源点的风险控制管理。
所谓事故预想预测,就是在事故未发生前,结合各自的操作岗位、操作设备、作业环境、作业人员等情况,进行危险因素辨识,假设事故发生后将会出现何种情景以及应该采取何种应对措施,做到胸有成竹,减少或降低事故发生时对人对物的伤害程度。例如,2007年,全厂结合易燃、易爆、易窒息的生产特点,以及氧气管道、氮气管道、放空管道等设备设施点长、面广的实际情况,组织各个基层单位开展事故预想预知工作,经多次研讨交流,分析制定了厂内《氧气管道、氮气窒息、气瓶作业危险部位、危险作业的控制方案》,明确了危险部位、作业环节、控制措施、涉及岗位人员、责任单位等内容,使各部门和各单位的职工更加清晰的知道在操作氧气管道、阀门,氧气放空,涉氧作业时的危险及预防措施。同时,针对事故预想预测,全厂各专业部门按照职责分工,制定了各项应急预案,并对氧气厂现有的16个应急预案分阶段进行了模拟演练和修改完善,大大提高了干部职工对氧气厂突发事故的应变能力。
首钢总公司搬迁调整计划启动后,氧气厂领导经过研究分析,制定了北京地区前期压产、减产生产运行计划,并分层次、分阶段进行了实施。氧气厂原有制氧机组8套,2007年以前,已经减产、封存了4套技术落后的制氧机组,仅保留了4套制氧机组交替运行。2007年,随着首钢总公司分阶段实施压产、减产工作的深入,氧气厂又停止运行了2套制氧机组。从2008年第2季度开始,氧气厂将再减产1套制氧机组,仅保留运行1套制氧机组。
在积极配合首钢总公司战略转移规划的同时,氧气厂在曹妃甸、首钢迁安钢铁厂、北京顺义冷轧项目对口筹建制氧工程中,抽调了大批技术人员、岗位操作人员、设备维修人员、安全管理人员,全力投入到新建项目的建设生产之中,进行安全培训、技术培训,不仅实现了北京地区压产、减产直至搬迁调整任务的顺利完成,而且保证了筹建项目的安全、顺利投产和人员合理安置就业的目标。(图片由温盛荣提供)
编辑 余茂君